The handling of heat generation in a large capacity blender, particularly when dealing with hot ingredients or extended blending times, is a critical aspect to consider. Here are some specific points to explore:
1.Cooling Mechanisms:
Ventilation Systems: A robust ventilation system is integral to managing heat in large capacity blenders. Inquire about the specifics, such as the size and placement of vents, and whether the blender employs active cooling mechanisms like fans. Understanding the engineering behind the ventilation system provides insights into how effectively the blender dissipates heat during prolonged blending, especially when tackling substantial quantities or dense mixtures.
2.Motor Efficiency:
Heat-Resistant Components: Explore the motor's construction materials in detail. High-quality, heat-resistant materials like advanced alloys or ceramics contribute to sustained motor efficiency under elevated temperatures. Delve into the specifics of these materials and how the motor's design optimizes heat dissipation, ensuring that it remains cool and performs reliably even during extended blending sessions with sizable loads or heat-intensive ingredients.
3.Thermal Protection:
Overheat Sensors: Delve into the sophistication of the blender's thermal protection mechanisms. Overheat sensors act as a proactive defense, promptly detecting deviations from safe temperatures. Understand the sensor's responsiveness, precision, and how it orchestrates an automatic shutdown to shield the motor and internal components from potential damage. This insight provides a deeper understanding of the blender's commitment to user safety and the longevity of its components.
4.Material Composition:
Heat-Dissipating Materials: Scrutinize the material composition of critical blender components. Materials with exceptional heat-dissipating properties, such as copper or aluminum, play a pivotal role in efficiently transferring heat away from crucial areas. Investigate how these materials are strategically integrated into the blender's architecture to create an effective heat management system, ensuring optimal performance even when confronted with demanding blending tasks.
5.Variable Speed Control:
Precision Blending Control: Interrogate the variable speed control system to understand its nuanced capabilities. It's not just about offering a range of speeds but providing users with precise control to match the demands of different ingredients. Inquire about the granularity of speed adjustments and how this feature allows users to tailor blending speeds, minimizing unnecessary heat buildup. This level of control is especially crucial when working with heat-sensitive or delicate ingredients.
6.Pre-Programmed Settings:
Optimized Blending Protocols: Unpack the sophistication behind pre-programmed settings. These settings go beyond mere convenience, often embodying optimized blending protocols for specific tasks. Investigate the intricacies of these protocols—how they're fine-tuned to achieve desired results with minimal heat generation. Understanding the synergy between pre-programmed settings and effective heat management provides a comprehensive view of the blender's efficiency in diverse blending scenarios.
7.Insulation:
External Insulation: Scrutinize the external design elements geared towards insulation. External insulation is pivotal not only for user safety but also for enhancing the overall blending experience. Explore how the blender shields users from accidental burns by preventing external surfaces from becoming excessively hot. This feature becomes paramount during extended blending sessions or when dealing with high-temperature ingredients, contributing to a user-friendly, safe, and efficient blending environment.
White large capacity blender
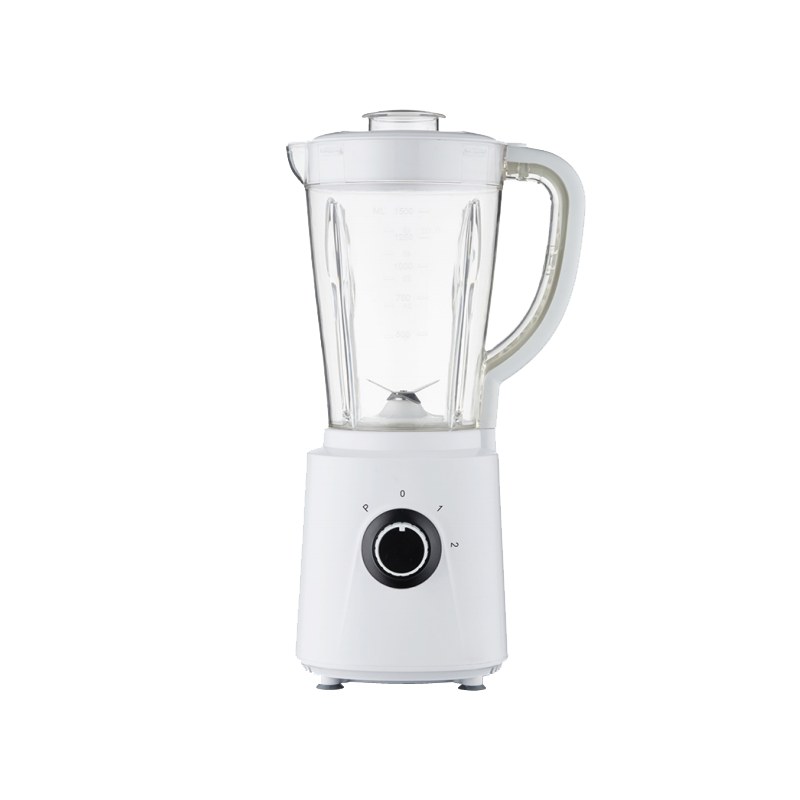
White large capacity blender
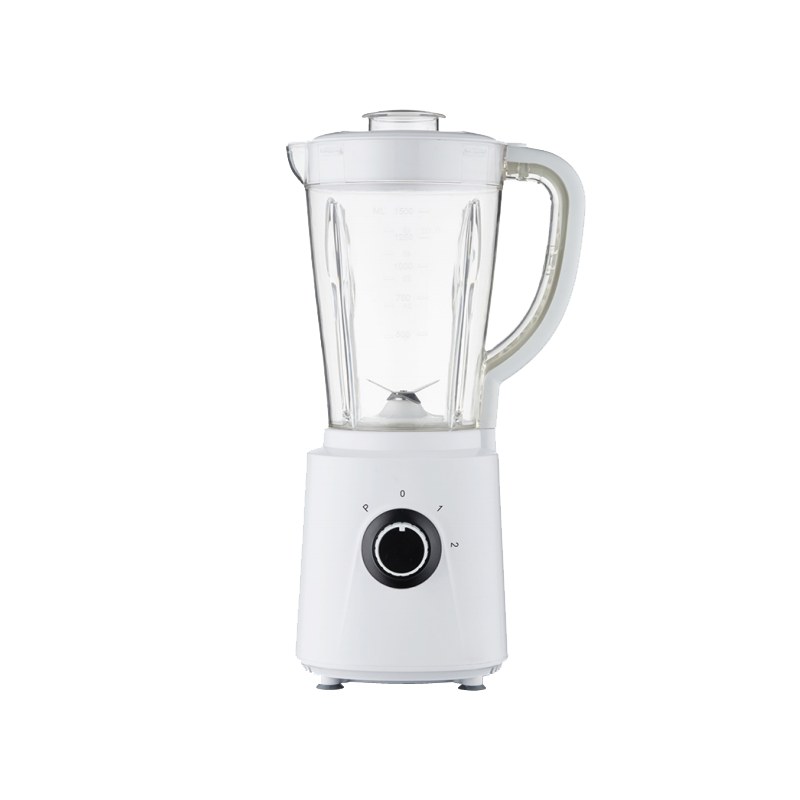